Adsorption cooling
Simply chill with waste heat.
Sustainable energy efficiency
Energy generation and consumption around the globe is still characterized by a very large efficiency deficit.
For example, about 30% of industrial energy input worldwide (8,862 TWh/a) is lost as waste heat, of which about 27% (2,422 TWh/a) is low-temperature waste heat between 60-100°C.
At the same time, about 17% of the electricity generated annually is used for refrigeration, resulting in CO2 emissions of about 2.24 Gt CO2e/a (6% of global emissions).
Adsorption chillers (AHPs) can use this waste heat for refrigeration and thus save significant CO2.
Refrigeration: a global electricity guzzler?
%
17% of the electricity worldwide goes into refrigeration
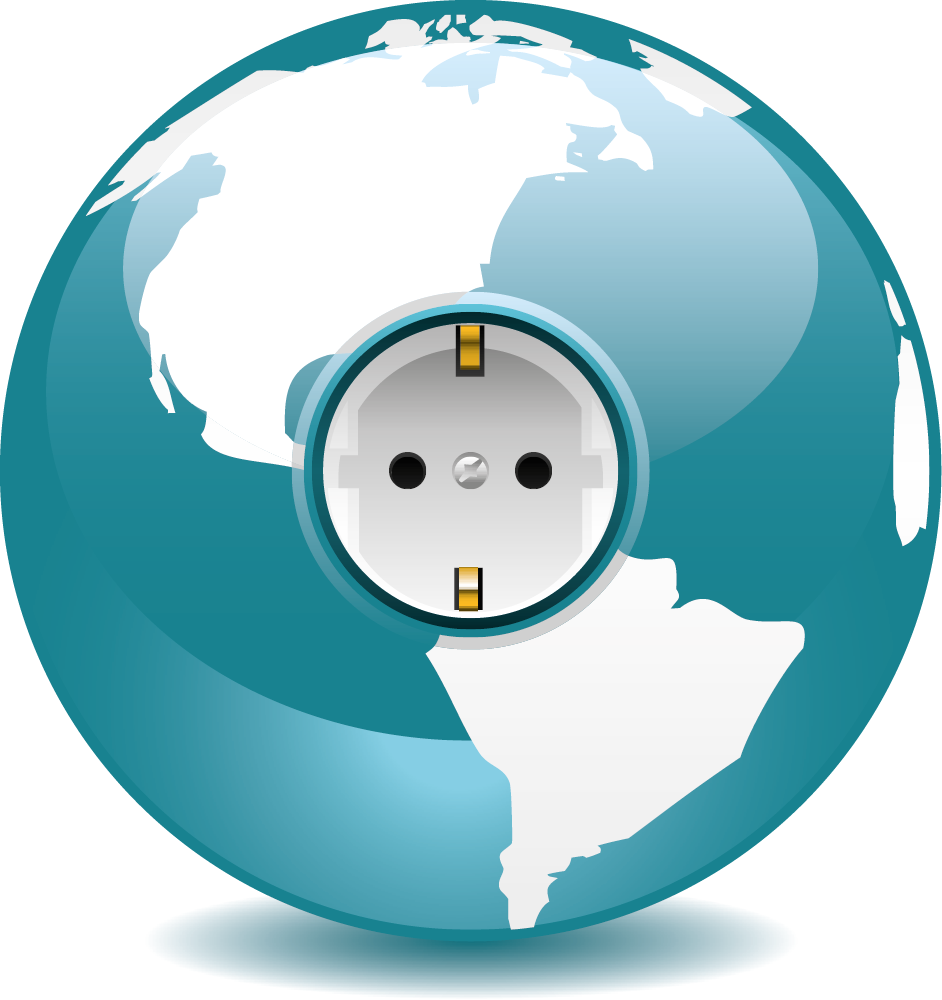
%
30% of industrial energy input is lost as waste heat
Using waste heat efficiently for refrigeration
Adsorption chillers are an alternative to conventional, electrically driven compression chillers for low-emission refrigeration.
Save 80% electricity
AHPs are driven by low-temperature waste heat (from 55 °C), saving around 80% electricity compared with conventional technologies.
Comparison of power consumption
- Conventional refrigeration 100%
- Adsorption refrigeration 20%
Adsorbus adsorption cooling helps to significantly reduce electricity consumption and CO2 emissions worldwide.
Refrigerant: Pure water
Artificial and fluorinated refrigerants will only be permitted to a very limited extent or not at all in the near future – and are therefore a dead end. In contrast, the use of natural refrigerants is being pushed by the federal government and the EU.
Advantage Adsorbus
Among the natural refrigerants, only water is non-flammable (like propane), non-toxic (like ammonia) and does not require high pressures (like CO2). Thus, adsorption technology is not only unique here, but has a clear advantage.
Continuous cooling
The adsorption process
To generate cooling, the water is evaporated in an evaporator while absorbing the heat flow at a low temperature. The evaporated water is then adsorbed by the adsorption material in the adsorber.
As soon as the adsorption material is fully loaded, it is regenerated.
For this purpose, the adsorption material is supplied with the required desorption heat via the waste heat flow. Subsequently, the expelled refrigerant vapour is condensed in the condenser and returned to the evaporator. Two adsorbers are used for continuous refrigeration, whereby the second adsorber operates anti-cyclically to the first adsorber.
Sustainable
- Water as refrigerant
- Quiet
- Oil-free
- Utilization of waste heat
- CO2 neutral cooling
Safe operation
- Few wearing parts
- No refrigerant losses due to vacuum process
- Vibration-free
Cost efficient
- Fast amortization
- Low energy costs
- Low maintenance
- BAFA eligible
Compliant safe
- Indoor installation unproblematic
- No F-gases regulation / pressure equipment directive
- None DIN EN 378
Industrial Cooling
-
Process engineering
-
H2 drying
-
Machine cooling
-
Plastics production
-
Food processing
-
Metal processing
Building Air Conditioning
-
Office buildings
-
Industrial halls
-
Commercial premises
-
Hospitals
Would you like to know more?
We look forward to being contacted by you!